Employee of the Year - 2023
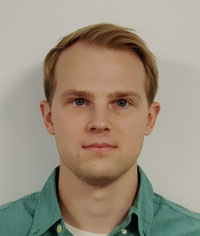
Benjamin Rauenbuehler
- Electronics Engineer
- Spangdahlem AB, Germany
- Executed daily support for 2371 sorties at Spangdahlem AB with 99.5% mission effective rate.
- Spearheaded numerous Spangdahlem maintenance actions including sixty-six 90-day inspections, thirty-two 180-day inspections, and forty component removals and installs.
- Maintained site operations amidst consistent low manning – site 57% staffed for 2nd half of year.
- Quickly mastered job tasks and processes upon being hired in Feb of 2023; subsequently made significant improvements resulting in being awarded Employee of the Quarter Q3-2023.
- Designed pod maintenance actions database; created 5 tracker spreadsheets to manage shop maintenance actions data and cross-check RAMPOD data.
- Actions Tracker: Records all maintenance actions and corresponding data and allows easy filtering for troubleshooting and reference. Single data entry populates four spreadsheets.
- Quickly resolved confusion with a pod cable harness serial number.
- PMI Tracker: Pulls information from the Actions Tracker to auto-update table showing when inspections are due for each pod, as well as current ETMs and cumulative hours.
- Corrected cumulative hour miscalculations in RAMPOD for 3 pods due to lost entries.
- Pod Inventory Tracker: Provides an auto-updated table of all serial numbers in each pod and highlights any inconsistencies with data in RAMPOD.
- Corrected 20 serial number discrepancies between shop data and RAMPOD.
- Led to recording 24 missing serial numbers, site now 100% SN tracking compliant.
- TCTO/Software Tracker: Keeps record of TCTOs for our pods.
- Corrected 34 discrepancies between shop data and RAMPOD.
- 180 Day Checklist: Produces an inspection report printout to use while inspecting pods. Automatically populates serial numbers for each component in pod (for verification).
- Developed a digital RTO Shot Log to replace handwritten shot log. This spreadsheet contains 50 unique buttons coded with over 500 unique lines of VBA code and shared USAFE wide.
- Faster, more accurate shot recording—20% faster, lower RTO workload and improved SA.
- Features include adjustable real-time Probability of Kill calculations, multiple, editable, simultaneous shot tracking, and manual override for pilots to meet desired learning objectives.
- Lauded by 52FW pilots for clean, easy to read logs and for auto generated statistics capture.
- Began development of digital SAM 1 shot log; final product will replace handwritten log, producing real-time auto-calculated results.
- Simulates SAM site alternating radar status and auto-calculates shot results.
- 30% faster shot recording, lower RTO/INTEL workload, and improved SA.
- Created and implemented a digitally automated pod loading tool.
- Ensures record keeping accuracy and improves pod loading efficiency, saving 1 hour per week.
- Advantages include sorting by location, auto-highlighting pods coming due for inspection, and autonomously showing pods available for loading and their total cumulative hours.
- Established a sortie tracker spreadsheet to function as a single source of data of all sorties.
- Organized to easily compare numbers to monthly sortie report and RAMPOD sorties.
- Includes a macro to export sortie data into the correct format for auto-import into RAMPOD.
- Saves at least 10 hours/month from previous system and reduces conflicts between reports.
- Developed and proposed new TD522 format. If implemented, could save each site at least 5 hours monthly and provide better data visualization for the company.
- Repurposed unused unit assets; provide all six employees new desks and monitors--saved $5.2K.
- Completed physical overhaul of site manager office layout and organization; lauded by PMR team.
- Stepped in as site computer specialist position; completed TARIF software updates on 16 devices.
- Streamlined cloning procedures; PGS refresh done 5 days early--increased productivity 20%.
- Troubleshot TARIF update issue on TGS computer--maintained cybersecurity compliance.
- Introduced various digital organizational efficiency changes to shop, including a shared task list, shared calendar for reoccurring tasks, and restructuring the site’s computer file structure.
- Initiated idea of sending monthly TARIF updates electronically; implemented DOD Wide.
- Process reduced cybersecurity incompliance; expedited software delivery lag up to 4 months.
- Key player in establishment of new LMOC room at Spangdahlem. Expanded and improved RTO capability and enabled use of MIDS-J, BOSS, and high-side feed in a central secure location.
- Led multi-agency site survey team--identified 3 potential sites.
- Sourced purchasing of equipment required for LMOC and COMM room.
- Routed networking cables through building to expedite LMOC communication network set-up.
- Set-up new furniture and equipment and routed/organized cables in LMOC and COMM rooms.
- Designed and fabricated four cases for KP-32s; saved over $400 and increased desk space.
- Executed Alternate Site Manager duties, single-handedly managed shop during Cobra Warrior EX.
- Led team in 52FW WarRoom $10K equipment purchase; prevented $3.7K in unnecessary costs.
- Coordinated sorties data collections with deployed units; fixed 10 errors.
- Spearheaded tech refresh: upgraded 5 of 6 computers and added 2 tablets for mobility tracking.
- Facilitated use of NIPR computers outside of office; enabled use while TDY--saved 20 hrs. monthly.
- COMSEC Officer; received zero discrepancies during AF COMSEC audit--awarded highest AF rating!
- Led pod team to achieve 99% sortie rate during Air Defender 23, largest exercise in NATO's history.
- Refurbished 19EWS UPS at Polygon; replaced batteries and saved USAF $1.5K in additional cost.
- Repaired intermittent RRU; replaced faulty parts with zero downtime to 52FW mission support.
- Supported pod testing on Tornado; ensure software fix for German aircraft deploying to Red Flag.
- Finished three self-improvement books on topics such as effective communication & habits.
- Continually learning VBA coding/excel functionalities, automated complex and tedious office tasks.
- Volunteered 120 hours to Cadence Int’l; improved MWR for local chapel associated organization.
- Designed and fabricated new coffee/serving bar, led weekly young adult group consisting of airmen and spouses, and served in the children’s ministries.
- Improved hands-on skills through woodworking hobby. Designed and built an 8-person oak dining table and chairs, TV low board, 2 end tables, a sofa table, and a glass piece display case.